Underwater inspection is a cornerstone of maintaining the safety, functionality, and longevity of structures submerged in water. From bridges spanning rivers to ships navigating oceans, offshore wind turbines harnessing renewable energy, dams controlling water flow, and navigation locks facilitating waterway transport, these assets are vital to global infrastructure. However, constant exposure to water subjects them to unique challenges like corrosion, erosion, and structural wear. Regular underwater inspections are essential to identify issues early, prevent catastrophic failures, and extend the lifespan of these structures. This article explores the importance of underwater inspection, the methods used, and how advanced technologies, such as UVision’s underwater 3D scanner, are transforming the field.
The Importance of Underwater Inspection
Underwater inspection involves assessing the condition of submerged structures to detect damage, corrosion, or other issues that could compromise safety or performance. These inspections are critical across multiple industries:
- Transportation: Ensuring bridges and locks remain safe for public use.
- Maritime: Maintaining ships to meet safety and regulatory standards.
- Energy: Keeping offshore wind turbines and dams operational.
- Civil Engineering: Monitoring infrastructure to prevent costly repairs or environmental damage.
By identifying problems early, underwater inspections reduce downtime, enhance safety, and support sustainability by extending the life of critical assets. As structures age—many dams in the United States, for example, are over 60 years old (USSD Dams) — the need for efficient and accurate inspection methods grows.
Current Methods for Underwater Inspection
Underwater inspection methods have evolved significantly, combining traditional techniques with cutting-edge technologies to improve safety, accuracy, and efficiency. Below are the primary methods used today:
Visual Inspection by Divers

Trained divers perform visual and tactile inspections, checking for visible damage, corrosion, or structural issues. This method is effective but can be labor-intensive, costly, and risky, especially in deep or hazardous waters. Divers often use underwater cameras to document findings, though poor visibility can limit effectiveness (TRID Bridge Inspection).
Remotely Operated Vehicles (ROVs) and Autonomous Underwater Vehicles (AUVs)
ROVs and AUVs are unmanned vehicles equipped with cameras, lights, and sensors. ROVs are controlled in real-time from the surface, while AUVs follow pre-programmed paths. These vehicles are ideal for inspecting deep or inaccessible areas, reducing risks to human divers. They are widely used for ships, wind turbines, and dams (Blueye Robotics).
Non-Destructive Testing (NDT)

NDT methods, such as ultrasonic testing, magnetic particle inspection (MPI), and eddy current testing (ECT), detect flaws in materials without causing damage. Ultrasonic thickness measurement (UTM) is commonly used to assess corrosion in ship hulls and bridge components. These techniques are critical for evaluating structural integrity (ScienceDirect Inspection).
Sonar and Imaging Technologies
Sonar systems, including side-scan and multibeam sonar, create detailed images of underwater environments, mapping structures and identifying anomalies. High-resolution cameras provide clear visuals for analysis. These technologies are essential for large-scale inspections, such as dam reservoirs or ship hulls (J.F. Brennan).
3D Scanning Technology
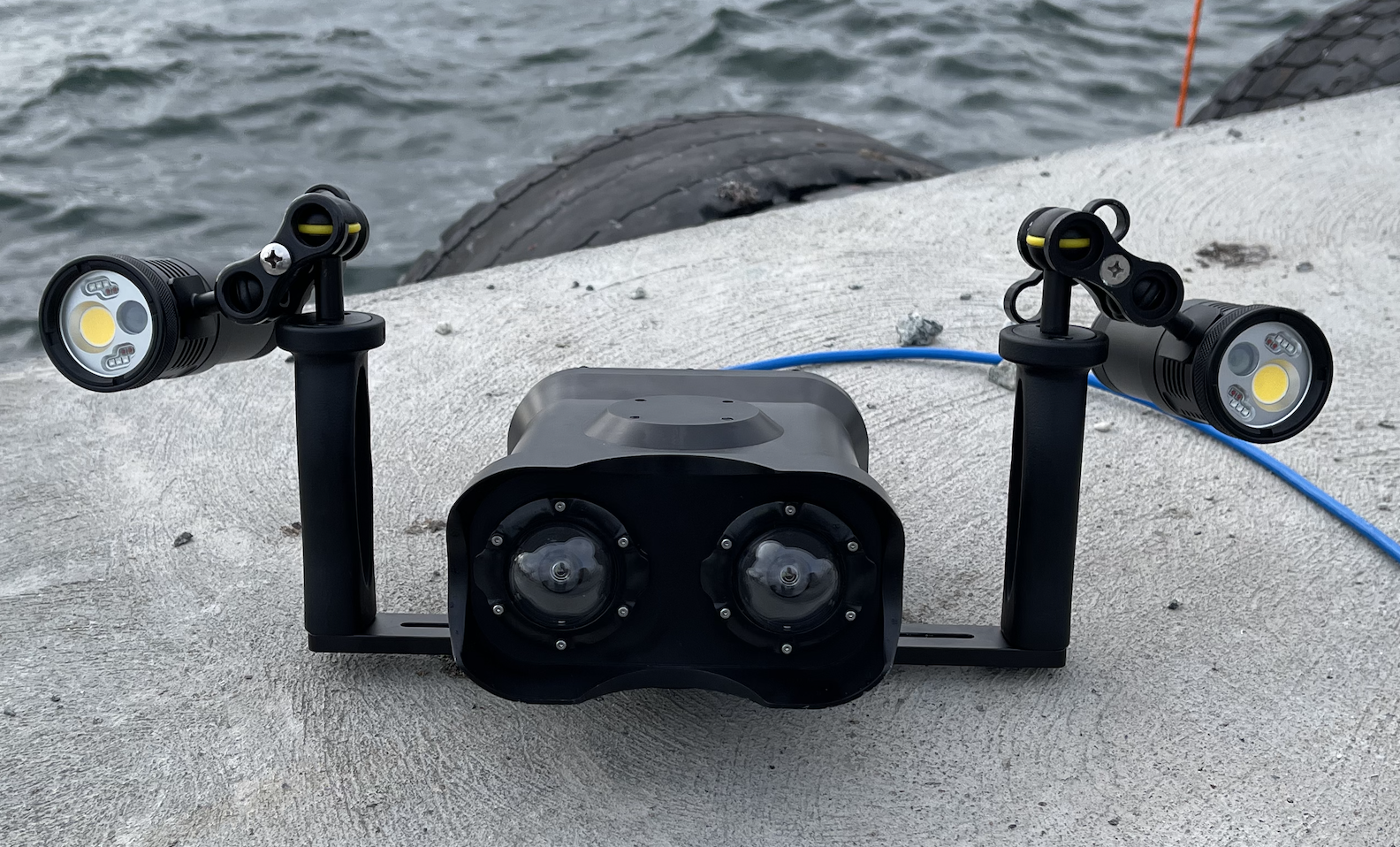
3D scanning represents a leap forward in underwater inspection. Devices like UVision’s underwater 3D scanner (UScanner) use advanced imaging and positioning data to create photorealistic 3D models with millimeter precision. These models allow for detailed analysis, precise measurements, and long-term monitoring, making them a game-changer for various inspection types. It can be mounted on ROVs/AUVs, mounted on a pole, or held by a diver.
Method | Advantages | Limitations |
---|---|---|
Visual Inspection (Divers) | Direct human assessment, tactile feedback | Risky, time-consuming, visibility issues |
ROVs/AUVs | Safe, deep-water access, real-time control | High equipment costs, operator training |
NDT | Detects hidden flaws, non-invasive | Requires specialized equipment |
Sonar/Imaging | Large-area coverage, detailed visuals | Limited in low-visibility conditions |
3D Scanning | High precision, real-time models, versatile | Initial investment, technical expertise |
Specific Types of Underwater Inspections
Each type of structure requires tailored inspection approaches due to its unique environment and function. Below, we explore the key inspection types, their purposes, and the methods employed.
Bridge Inspection
Bridges crossing waterways have critical submerged components, such as piers, abutments, and foundations, which are prone to scour (erosion around foundations), corrosion, and structural deterioration. The National Bridge Inspection Standards (NBIS) mandate underwater inspections every 60 months (F&V Engineering). Methods include:
- Visual and Tactile Inspections: Divers check for scour and damage, often in low-visibility conditions.
- NDT: Ultrasonic testing assesses material thickness and integrity.
- 3D Scanning: UVision’s scanner creates models to monitor scour progression, aiding long-term maintenance (UVision Bridge Use Case).
Scour is the leading cause of bridge failures, making these inspections vital for public safety. Read our comprehensive guide to underwater bridge inspections.
Ship Inspection
Ships require regular underwater inspections to assess hulls, propellers, and rudders, ensuring safety, regulatory compliance, and operational efficiency. Inspections are conducted for pre-purchase evaluations, financing, or maintenance planning (Sinotech Marine). Methods include:
- Visual Inspections: Divers or ROVs check for damage or biofouling.
- UTM: Measures hull thickness to detect corrosion.
- Sonar and CCTV: Provides comprehensive hull views.
- 3D Scanning: UVision’s scanner creates detailed hull models for precise damage assessment.
Underwater inspections in lieu of dry-docking (UWILD) are increasingly popular for their cost-effectiveness and efficiency.
Wind Turbine Inspection
Offshore wind turbines face harsh marine environments, requiring inspections of foundations, cables, and submerged structures to ensure operational efficiency and safety. Regular assessments prevent costly downtime and support renewable energy goals (TSC Subsea). Methods include:
- ROVs: Equipped with cameras and sensors for deep-water inspections.
- NDT: Techniques like Alternating Current Field Measurement (ACFM) detect weld cracks.
- 3D Scanning: UVision’s scanner provides high-resolution models to identify defects, reducing diver deployments (UVision Wind Turbine Use Case).
Dam Inspection
Dams are critical for water management, but their submerged components, such as intake structures, gates, and spillways, are susceptible to cracks, leaks, and concrete degradation. Inspections are essential for safety and compliance with regulations like FERC Part 12 (J.F. Brennan). Methods include:
- Diver Inspections: Assess visible damage and gate functionality.
- ROVs: Survey hard-to-reach areas.
- Sonar and Hydrographic Surveys: Map reservoirs and detect silt buildup.
- NDT: Evaluates material integrity.
- 3D Scanning: Creates comprehensive models for detailed analysis.
Lock Inspection
Navigation locks facilitate waterway transport by raising or lowering boats between different water levels. Inspections focus on gates, seals, and chambers to ensure functionality and prevent leaks. Methods include:
- Visual Inspections: Divers or ROVs check for wear and damage.
- NDT: Assesses structural integrity of metal components.
- 3D Scanning: Provides precise models to monitor gate and chamber conditions (UVision Lock Use Case).
Locks are critical for efficient waterway navigation, and regular inspections ensure uninterrupted operations.
The Role of UVision’s Underwater 3D Scanner
The UVision UScanner is a state-of-the-art tool transforming underwater inspection across multiple sectors. Priced starting at €13,900 ex.VAT, the scanner combines high-quality imaging with precise positioning data to create photorealistic 3D models with millimeter accuracy (UVision UScanner). Key features include:
- Global Shutter Stereo Camera: Captures images with minimal distortion, ideal for low-visibility conditions.
- Real-Time Processing: Generates 3D point clouds during scans, guiding operators and ensuring complete coverage.
- Versatile Mounting: Can be ROV-mounted, pole-mounted, or handheld by divers, adapting to various scenarios.
- Durable Design: Corrosion-resistant aluminum casing, rated for 300m depth.
- User-Friendly Interface: Integrated hardware and software streamline data collection and model generation.
The scanner’s applications are vast, from detecting scour around bridge foundations to assessing ship hull damage and monitoring wind turbine foundations. By reducing the need for frequent diver deployments, it lowers costs and risks while providing unparalleled detail for maintenance planning.
Conclusion
Underwater inspection is vital for maintaining the safety and sustainability of critical infrastructure. Traditional methods like diver inspections and ROVs remain essential, but advanced technologies like UVision’s underwater 3D scanner are revolutionizing the field. Offering precision, efficiency, and versatility, 3D scanning enhances inspection outcomes across bridges, ships, wind turbines, dams, and locks. As technology continues to advance, the future of underwater inspection promises even greater safety, cost-effectiveness, and environmental protection, ensuring our submerged assets remain robust for years to come.